|
|
|
|
|
|
WIRELESS DATA MONITORING SYSTEMS FOR CRANES
| | |
|
|
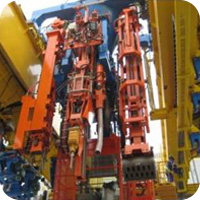 |
Multiple cranes separated in different operation area, operated individually from the operator cabin and used for multitasks like removing anode and cathode from the pot, filling the pot with bath at open places, traveling a distance of 1.2 km to handle all the pots in a room, for removing broken pieces from the pot and many other operation like steel, Cement industry etc.
Being most important part of a metal industry, down time for the crane machine is not affordable by the industry. Being operated individually, requires more time to acknowledge any fault to a maintenance engineer, takes a time for an maintenance people to find out the problem and troubleshooting for the fault and preparing the machine ready for operation. The reduced operating hour affects the production drastically and hence the solution is required to reduce the machine breakdown time.
Solution to above condition is to monitor all the cranes from the central location where a maintenance person can keep his eye on all the machines and can short out the exact problem behind the crane breakdown. Again physical connectivity between all the moving cranes is a big milestone and wireless connectivity in a high EMC area, dusty environment, Close Structure etc was a question.
So Wireless connection is designed using Mesh technology between access point and moving clients for seamless connectivity.
Features
Online monitoring of all cranes and their tools’ operation
Reduce breakdown/downtime with preventive maintenance
Instant alarm messages for critical condition
High connectivity of all the wireless modules with turbo roaming technology
Wireless download/upload of PLC program
Alarm and Faults observation from control room
Analysis of frequent alarm and faults through Historian Reports
Fiber optic connectivity for longer distance & highly EMC area.
Benefits
Continuous monitoring of all cranes from centralized SCADA reduces the time for notifying the fault condition from an operator to a maintenance engineer and hence reduced MTTR
Monthly analysis of historical data can be useful to reduce future faults
Frequent alarm of particular tool/part can be used to prevent future failure of a tool/part with preventive action
Operator skills are evaluated with real time animation of crane operation
With prior information about motor run time and maintenance schedule, an emergency breakdown can be prevented
Direct sending of critical alarms to senior management via SMS
Maintenance log book with specific pattern and category can be utilized for an untrained people, who can take reference of previous solution for same kind of problem
Documents:
PDF:Click Here For DownLoad
DataSheet:
|
| |
|
|
|
|
|
|
|
|
|
|